Industry 4.0 Technologies: IoT in Engineering
Industry 4.0 technologies aim to enhance productivity, efficiency, and flexibility while enabling more intelligent decision-making and customization in manufacturing and supply chain.
Engineering
April 26, 2024
9 minutes read
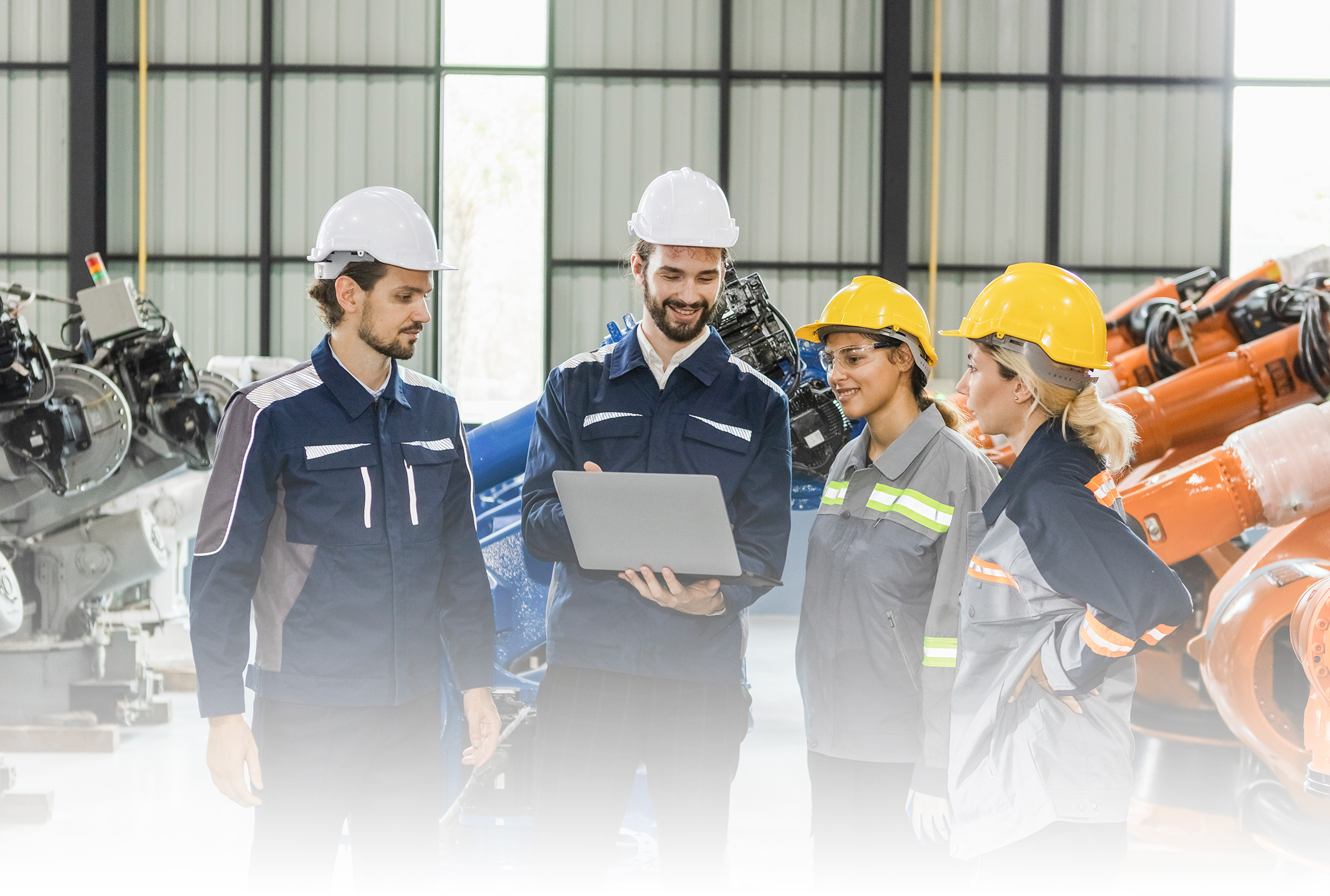
“”
Industry 4.0 enables companies to become more agile and faster in decision-making and troubleshooting. It can help align various departments or functions to interact in analysis and decision-making.
Industry 4.0 technologies facilitate the integration of intelligent digital technologies into manufacturing and industrial processes. The new Industrial Revolution features the use of automation, advanced data analytics, and smart and autonomous systems. IoT in engineering and other industry 4.0 technologies have the potential to revolutionize global business and transform the skill sets of the workforce. This is a significant transformation regarding the way we produce products thanks to the digitization of manufacturing.
What is industry 4.0?
Industry 4.0, also known as the Fourth Industrial Revolution, represents the era we are living in. This era is marked by connectivity, advanced analytics, automation, and advanced-manufacturing technology.
The most distinguish characteristic of the industry 4.0, compared to previous eras is the integration of intelligent digital technologies into manufacturing and industrial processes.
Industry 4.0 technologies revolutionize the automation, monitoring, and analysis of supply chains through smart technology. This enables smart manufacturing and the creation of intelligent factories.
What are the 9 pillars of industry 4.0?
Industry 4.0 is built on nine technology pillars that bridge the physical and digital worlds. This pillars help make smart and autonomous systems possible. These innovations allow for seamless integration of various systems, tools, and innovations.
Big Data and Analytics: Big data is the use of large data sets to optimize manufacturing and business processes.
Augmented Reality: Augmented reality overlays digital imagery onto the real world, enhancing visualization and interaction.
Simulation: Creating virtual environments to analyze and optimize production processes.
Internet of Things (IoT): IoT in engineering involves connecting devices and systems to enable real-time communication and decision-making.
Cloud Computing: Using remote servers to store, manage, and process manufacturing data, enabling scalability and collaboration.
Additive Manufacturing (3D Printing): Producing customized components and products efficiently and sustainably.
Cyber-Physical Systems: Integrating physical systems with embedded electronics for intelligent operations.
Artificial Intelligence and Machine Learning: Implementing algorithms to simulate human intelligence and optimize processes.
System Integration: Interconnecting factory equipment, sensors, and software platforms to operate as a unified system.
What are some examples of industry 4.0 technologies?
Industry 4.0 technologies are transforming manufacturing and industrial processes, enabling greater connectivity, intelligence, and automation, and improving efficiency, productivity, and flexibility. Emerging trends in engineering for industry 4.0 include:
Big Data and Analytics: Big data and analytics are the collection and analysis of massive amounts of data from various sources. This includes factory equipment, IoT devices, ERP and CRM systems, and weather and traffic apps. This data helps provide accurate, actionable insights for decision-making.
Autonomous Robots: These are robots that can perform tasks without human intervention. These tasks include assembly, packaging, and inspection, to improve efficiency and productivity.
Digital Twins: Digital twins are virtual models of physical systems. These simulations can be done for machines and processes, to simulate and optimize their performance.
Augmented Reality (AR): The integration of digital information into the physical environment, allowing for real-time data visualization and interaction. This improves decision-making and productivity.
Cloud Computing: Cloud computing is the use of remote servers to store and process data. It enables real-time access and collaboration, and reducing the need for on-site infrastructure.
Additive Manufacturing (3D Printing): The production of physical objects from digital models, enabling rapid prototyping, customization, and mass production.
Advanced Robotics: The use of advanced robots, such as collaborative robots (cobots), can help perform complex tasks. This robots work alongside humans, improving safety and efficiency.
Artificial Intelligence (AI) and Machine Learning (ML): Machine learning and artificial intelligence in engineering are the use of algorithms and models to simulate human intelligence and decision-making. It enables predictive maintenance, quality control, and other applications.
Cyber-Physical Systems (CPS): This is the integration of physical systems with digital technologies, such as sensors and actuators, to enable real-time monitoring and control.
Internet of Things (IoT): The IoT is a network of interconnected devices, sensors, and systems. It allows for real-time communication and data exchange, improving efficiency and productivity.
How is industry 4.0 changing the manufacturing industry?
Industry 4.0 technologies are transforming the manufacturing industry by integrating intelligent digital technologies into manufacturing and industrial processes. This is revolutionizing automation, monitoring, and analysis of supply chains. The key technologies involved include IoT in engineering, AI, advanced data analytics, robotics, and automation. All these technologies which smart manufacturing and the creation of intelligent factories.
Industry 4.0 technologies aim to enhance productivity, efficiency, and flexibility while enabling more intelligent decision-making and customization in manufacturing and supply chain.
The integration of these technologies has led to significant improvements in manufacturing, including increased automation, predictive maintenance, self-optimization of process improvements.
Industry 4.0 concepts and technologies can be applied across all types of industrial companies. Companies can greatly benefit from the help of an engineering consulting companies for the integration of this technology in their processes and infrastructures.
How is IoT in engineering defining industry 4.0?
IoT is a key enabler of Industry 4.0 in the manufacturing industry. IoT in engineering allows for the creation of smart factories that are more efficient and productive. By using IoT-enabled devices and integrating them within manufacturing processes, companies can gather real-time data on assets.
Industry 4.0 enables companies to become more agile and faster in decision-making and troubleshooting. It can help align various departments or functions to interact in analysis and decision-making. Predictive modeling helps in predicting and forecasting key performance indicators of assets and processes. This allows for better planning, scheduling, and improving production efficiency and reducing operational and maintenance costs.
The integration of IoT in the manufacturing industry is a crucial part of the Industry 4.0 revolution. It helps bridge the gap between IT and OT systems, enabling bidirectional data transfer to ERP and cloud. This integration allows for improved plant visibility, quality, efficiency in inventory management and production scheduling, and meeting compliance requirements, product innovation, and speed.
In summary, IoT is a crucial technology in defining Industry 4.0 in the manufacturing industry. The integration of IoT in engineering enables the creation of smart factories, improving efficiency, productivity, and decision-making. Combined, this can help close the gap between IT and OT systems. The integration of IoT in the manufacturing industry is a significant part of the Industry 4.0 revolution, with manufacturers investing heavily in digitization efforts towards smart factories and connectivity.
How can engineering companies integrate IoT in their processes?
Engineering companies can integrate IoT by leveraging a variety of strategies and technologies to enhance their operations and services. Here are some key ways in which engineering companies can integrate IoT:
Utilizing IoT-enabled Devices: Engineering firms can incorporate IoT-enabled devices such as sensors and controllers to track and monitor various aspects of their operations. This will allow real-time data collection and analysis.
Implementing IoT Platforms: By adopting IoT platforms, engineering companies can connect lower-level sensors, systems, machines, and control systems, facilitating bidirectional data transfer to ERP and cloud systems, bridging the gap between IT and OT systems.
Enhancing Plant Visibility: IoT integration can improve plant visibility, quality control, inventory management, and production scheduling by connecting to sensors, machines, and control systems, enabling better decision-making and efficiency.
Leveraging Predictive Modeling: Engineering companies can use IoT for predictive modeling to forecast key performance indicators of assets and processes, aiding in better planning, scheduling, and production efficiency.
Enabling Real-time Monitoring and Control: IoT integration allows for real-time monitoring and control of systems and processes, enabling faster decision-making and troubleshooting, aligning various departments for improved analysis and decision-making.
Exploring New Ideas and Processes: IoT can support industrial engineering in developing new ideas and processes by conceptualizing technology applications and exploring innovative solutions.
Augmenting Current Projects: IoT applications in industrial engineering can augment current projects by adding new layers of observability and collecting data for better insights and decision-making.
Executing Control Elements: IoT systems can include control elements to execute tasks, such as programming systems to control processes and augmenting operations with advanced tracking and monitoring capabilities.
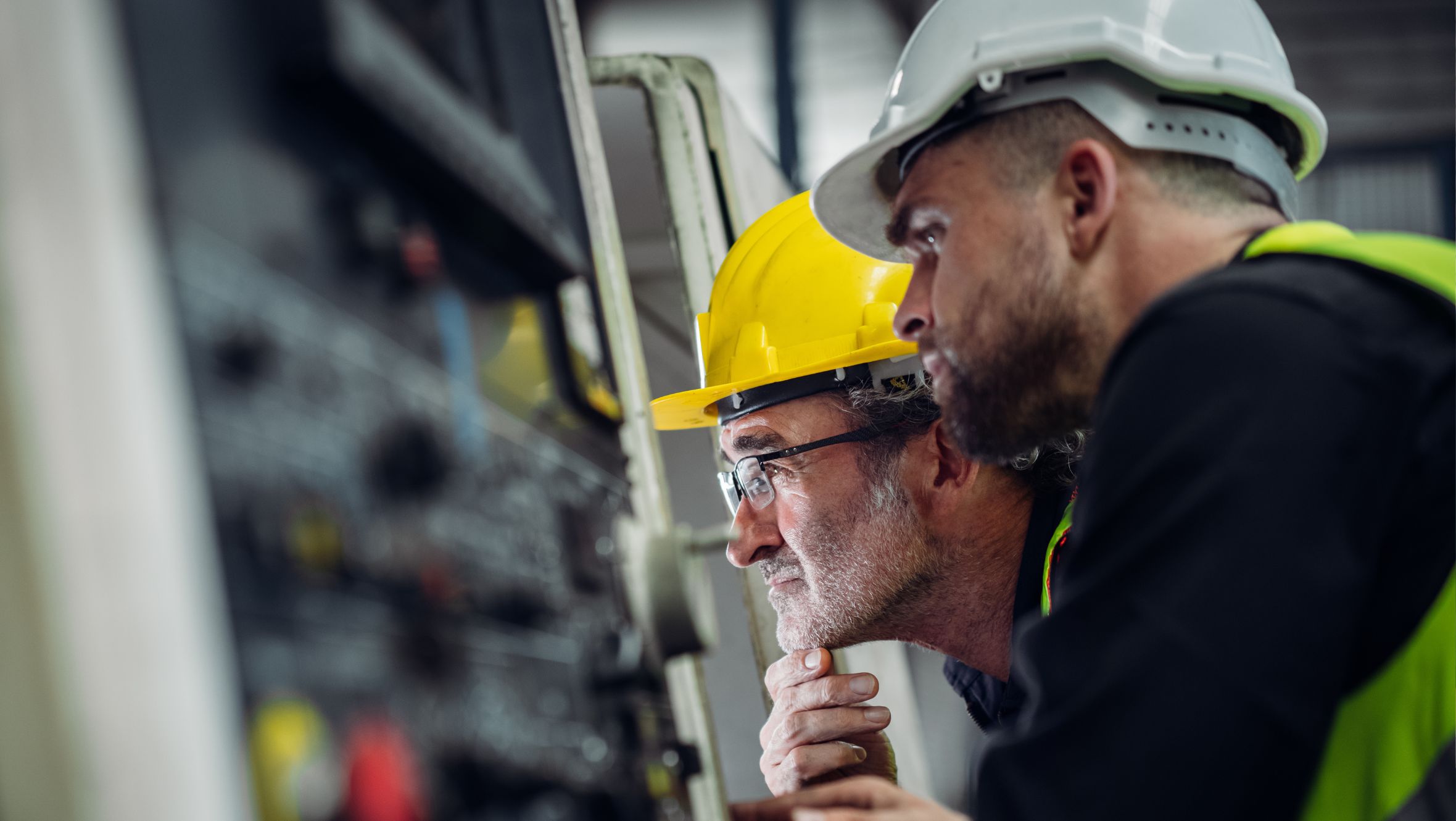