From Coal to Black Pellets: A Sustainable Solution for Energy Production
Prime Engineering France plays a pivotal role in sustainable solutions, contributing their expertise in the energy sector to support the development of efficient and innovative factories in France and throughout.
Case Study
November 20, 2023
9 minutes read

“”
In addition to overseeing the production of these biomass briquettes, the globality of the project also encompasses coordination between the factory and the waste-to-energy company, which is Prime Engineering’s client in this project.
In response to the urgent need to reduce greenhouse gas emissions and combat climate change, Prime Group partnered with a French energy company to develop a sustainable waste-to-energy solution. The goal was to replace coal production and usage with a cleaner and more efficient fuel source, black pellets, thereby reducing the factory’s carbon footprint and environmental impact.
Through a collaborative effort and innovative engineering, we were able to successfully implement this solution and achieve significant benefits for both the factory and the environment. This case study provides a detailed account of our waste-to-energy project, its aims and applications, and the positive outcomes it generated.
The Need for Sustainable Energy Solutions
The need for sustainable energy solutions arises from the environmental impact of traditional energy sources, such as coal, oil, and gas. These non-renewable energy resources contribute to climate change, air pollution, and other environmental problems. In addition, they are finite resources that will eventually run out, still the majority of energy production in the world is still dependent on these resources.
The energy and environment sector has seen a crescent demand for clean energy sources, such as wind, solar, and biomass. This resources offer a cleaner and more renewable alternative to traditional sources, helping to reduce carbon emissions and promote a cleaner environment for future generations. It was from this premise that the need to create the first energy factory fueled by biomass briquettes arose.
The Black Pellet Project: A Sustainable Alternative to Coal
The solution that Prime Engineering and our two partners – the EDF factory, and the waste-to-energy company – settled on was black pellets, biomass briquettes that are made from compressed wood residues and other biomass sources. They have a high energy density and low moisture content, making them an efficient and sustainable alternative to other non-renewable energy resources. When burned, they release significantly fewer pollutants and greenhouse gases into the atmosphere compared to coal, which makes them an attractive option for reducing the carbon footprint of energy production.
Project Implementation and Results
In the endeavor to transition from coal to black pellets, the project underwent a meticulous implementation process marked by strategic planning and innovative solutions. The initial phase involved in-depth research and development, assessing the viability of black pellets as a sustainable alternative. Collaborative efforts between Prime Engineering, the factory, and the waste-to-energy company paved the way for a seamless transition.
Key Milestones
The project kicked off with comprehensive research to identify suitable biomass sources for black pellet production. Engineers at Prime Engineering employed cutting-edge techniques in biomass processing, ensuring optimal energy density and low moisture content. The successful collaboration between the project partners led to the establishment of efficient manufacturing processes, resulting in the production of high-quality black pellets.
Outcomes Achieved:
The transition from coal to black pellets will yield remarkable outcomes. Carbon emissions were significantly reduced, aligning the factory with eco-friendly practices. Ideally, the environmental impact assessments will showcase a substantial decrease in pollutants, emphasizing the project’s positive contribution to air quality. Additionally, the energy efficiency of the factory will face notable improvements, marking a pivotal step toward sustainable energy production.
Project Steps
1. Planning and Research:
The project commenced with a thorough planning phase, where experts analyzed the feasibility of black pellets as a viable energy source. Extensive research was conducted to identify the appropriate biomass materials and manufacturing techniques.
2. Collaboration and Engineering:
Prime Engineering facilitated seamless collaboration between the factory and the client. Engineers employed advanced methods to compress wood residues and biomass into black pellets. Rigorous testing and quality control measures were implemented to ensure the pellets met industry standards.
3. Implementation and Transition:
During the implementation phase, existing coal-based systems were gradually replaced with those compatible with black pellets. Precise engineering solutions were employed to integrate the new energy source seamlessly. Thorough testing and adjustments were made to optimize performance.
Possible Challenges
1. Technical Hurdles:
Adapting the factory’s infrastructure to accommodate black pellets posed technical challenges. Engineers devised innovative solutions to retrofit existing equipment, ensuring a smooth transition without compromising efficiency.
2. Regulatory Compliance:
Navigating regulatory requirements and ensuring compliance with environmental standards presented challenges. Close coordination with regulatory bodies and adherence to stringent guidelines were essential in overcoming these hurdles.
3. Supply Chain Logistics:
Managing the steady supply of biomass materials for black pellet production required efficient logistics. Strategic partnerships were established with suppliers, ensuring a consistent flow of raw materials to sustain the manufacturing process.
Next Steps
Ongoing efforts include regular monitoring of the factory’s operations to maintain optimal performance. Continuous improvement initiatives are in place to enhance green energy efficiency further and reduce the environmental footprint. Additionally, discussions are underway for potential expansions and similar projects in other locations, indicating a commitment to replicating the success of this initiative on a broader scale.
In conclusion, the project’s implementation showcased the transformative power of sustainable energy solutions. By overcoming challenges and embracing innovative approaches, such as the transition from coal to waste-to-energy solutions, as black pellets, will not only reduced the factory’s carbon footprint but also set a precedent for environmentally conscious energy production. As the project continues to evolve, it serves as a beacon of inspiration for future endeavors in the realm of sustainable energy production.
Prime Engineering’s Role as Project Director
Prime Engineering was involved with this project from the get-go, having been involved with three engineers, including the Head of the Project and the Project Manager. The initial goal of this project was to take one of France’s energy factories, fueled by coal, and to take a waste-to-energy solution that could serve as a clean energy solution for it.
In addition to overseeing the production of these biomass briquettes, the globality of the project also encompasses coordination between the factory and the waste-to-energy company, which is Prime Engineering’s client in this project. This coordination is also dependent on ensuring that timelines are met and making sure that the facility is respecting to the required specifications.
With our extensive experience in managing large-scale projects, the Head of the Project is well-equipped to ensure that the project is completed on time and within budget. Furthermore, he will need to navigate a complex political landscape as he works to get the project off the ground, as this is the first factory in the world to update from coal to biomass briquettes – a relatively new energy resource. As such, this involved liaising with the ministry and Dreal, as well as working closely with staff at the coal-fired power station as the transition into black pellet is moving.
Conclusion: The Future of Sustainable Energy Production
Simultaneously with this project, in late 2023, the waste management and recycling company based in France is consolidating its plant engineering operations, merging its existing teams with those acquired through recent acquisitions.
The newly formed business unit will integrate plant engineering teams from various entities according to the company’s announcement. Additionally, the group unveiled its proposal for a waste-to-energy plant to be constructed near Perth in Scotland, as part of a collaboration with a local waste management organization.
We can assume that the future of production revolves heavily around sustainable solutions, namely waste-to-energy. As we see more factories waste-to-energy factories emerging around Europe and the World, we will realize its impacts and drift to more sustainable alternatives.
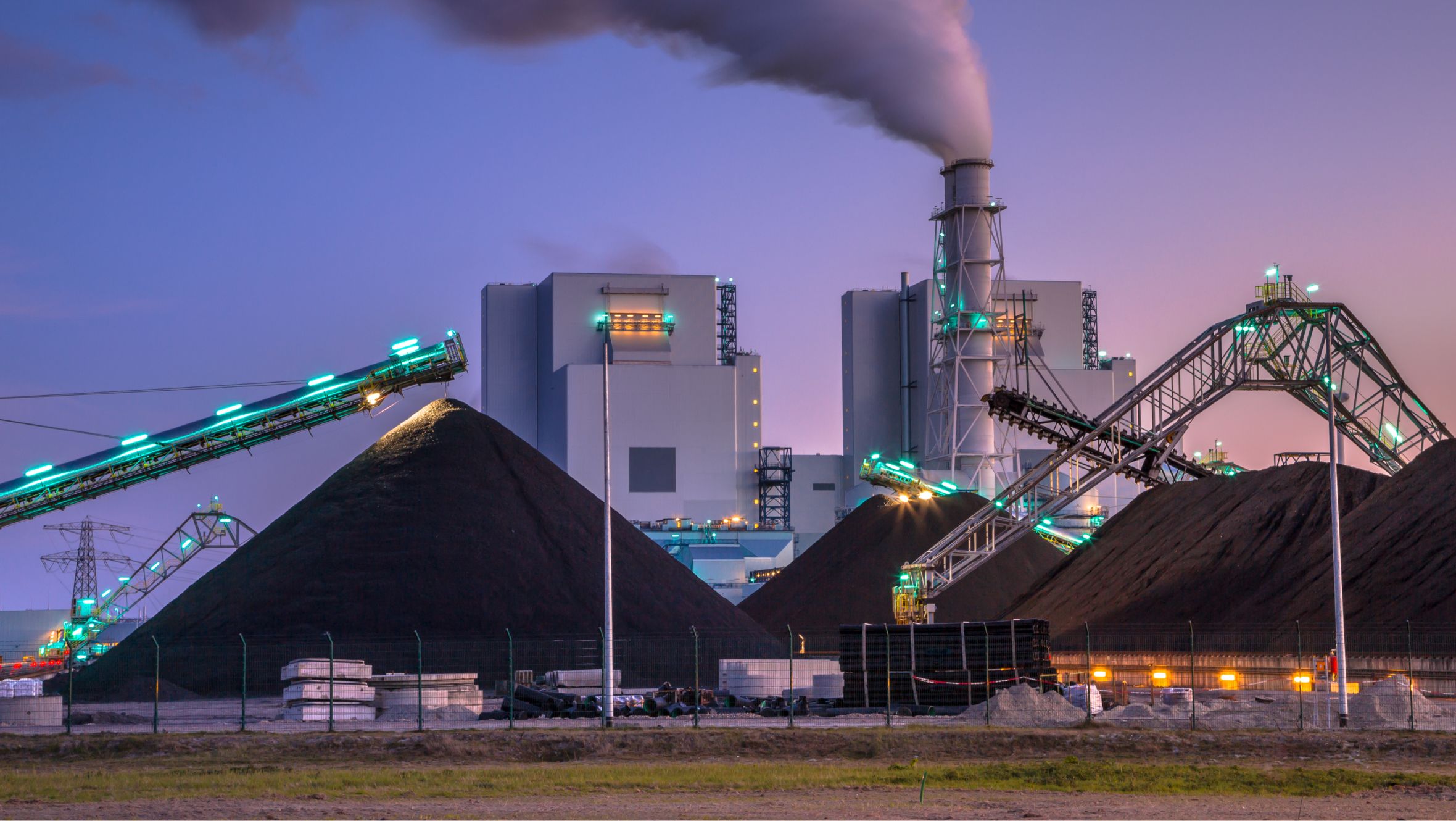