Case Study: Digital Transformation in a Manufacturing Environment
This case study explores the challenges encountered, the innovative solutions implemented, and the profound impact of digitalization on their manufacturing processes.
Case Study
August 22, 2024
6 minutes read
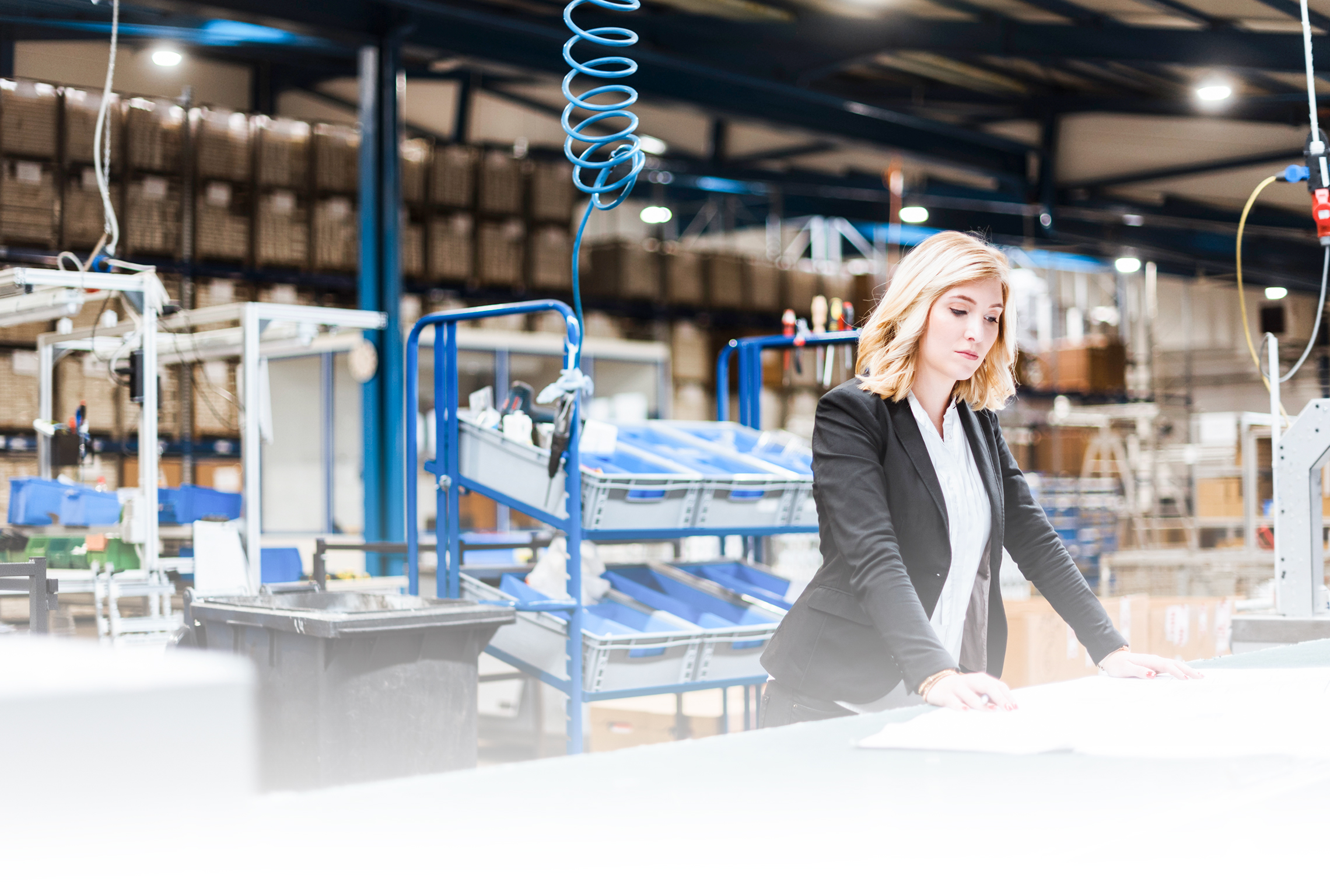
“”
The implementation of the Proplan and Shop Floor applications significantly improved the efficiency of the group’s production processes.
In manufacturing environments, the ability to adapt and innovate is critical for maintaining competitive advantage. Our client, a leading producer of ceramics, recognized the need to modernize its production processes across multiple factories. Faced with the challenge of managing complex workflows and meeting increasing customer demands, the company turned to digital solutions to enhance efficiency, streamline operations, and gain better control over its production environment. Partnering with InnoTech, the client embarked on a journey of digital transformation, leveraging cutting-edge tools to revolutionize its approach to planning, execution, and production management.
This case study explores the challenges encountered, the innovative solutions implemented, and the profound impact of digitalization on their manufacturing processes.
Technology and Tools Used
Proplan Application for Planning:
This prevalent ceramics manufacturer partnered with InnoTech to develop the Proplan application, which replaced traditional Excel spreadsheets for planning production processes. The Proplan app was designed using the .NET Framework and C#, featuring a WPF-based desktop interface for a seamless user experience. The application followed a client-server architecture, with SQL utilized for data modeling. Proplan systematically organized production stages for each order, considering variables like piece characteristics, glazing requirements, and machine availability.
Shop Floor Application:
In late 2022, another tool was introduced—a Shop Floor Application designed to integrate with the Proplan system. This application provided real-time visibility into production schedules and tasks, with each machine equipped with a monitor to display upcoming tasks based on planning data. The application also tracked the movement of pieces between machines, ensuring better control and optimization of production processes.
Process Improvement
Streamlining Production Planning:
Before the introduction of Proplan, the production planning process at the client’s facilities was managed through Excel and paper sheets. These methods were not only inefficient but also cumbersome, especially when dealing with complex workflows across four factories. The Proplan application streamlined the planning process by facilitating manual planning execution, significantly reducing the time required for planning tasks and eliminating the issues caused by the slow response times of Excel when handling large data volumes.
Enhancing Production Flow on the Shop Floor:
The Shop Floor Application enhanced process visibility by enabling real-time tracking of piece movements between machines. By strategically installing monitors on the shop floor, the application provided operators with timely information about upcoming tasks, which reduced downtime and ensured a smoother production flow. This real-time visibility was crucial in managing and optimizing the production process, ensuring that each machine and operator could function more efficiently.
Team Collaboration
Collaborative Development and Scalability:
The successful implementation of these digital tools was a result of a strong collaboration between the client and InnoTech. The project began with a Solution Architect and, as the need for more expertise arose, the team was scaled up or down according to the demands of the project. At one point, the team included not only the Solution Architect but also a Developer and a UX/UI expert, highlighting the flexible and scalable approach that was vital to the project’s success.
Continuous Feedback and Iteration:
Both applications—Proplan and the Shop Floor Application—were developed and tested in close collaboration with the production team. Continuous feedback was sought to refine the applications, especially during the deployment of the Shop Floor Application in the fourth factory. This iterative process ensured that the tools met the practical needs of the factory floor while also being user-friendly and efficient.
Innovation
Replacing Traditional Methods with Digital Tools:
The Proplan application was a significant innovation for the client, replacing outdated and inefficient Excel-based methods with a robust digital solution. This transition to a digital tool not only modernized the planning process but also laid the groundwork for further innovations, such as the integration of real-time shop floor management.
User-Centric Design in a Challenging Environment:
Given the challenging environment of the factory floor, where digital tools are often less effective, special attention was paid to UX/UI design. The user experience review conducted by the company informed the development of user-friendly interfaces that were both intuitive and resilient to the demands of the manufacturing environment. This focus on usability ensured that the digital tools were not only effective but also embraced by the end-users.
Results and Impact
Improved Efficiency and Production Control:
The implementation of the Proplan and Shop Floor applications significantly improved the efficiency of the group’s production processes. The digital tools enabled better planning, execution, and control, leading to a more streamlined workflow and reduced downtime. With real-time visibility into production schedules and piece movements, the company could optimize its operations, ultimately resulting in enhanced customer satisfaction.
Scalable Solutions for Future Growth:
These digital tools provided the ceramics group with scalable solutions that could adapt to future demands. The success of the Proplan application led to the development of the Shop Floor Application, showcasing the potential for continued innovation and improvement. The ability to scale the project team according to the evolving needs of the company further demonstrated the flexibility and sustainability of the solutions implemented.
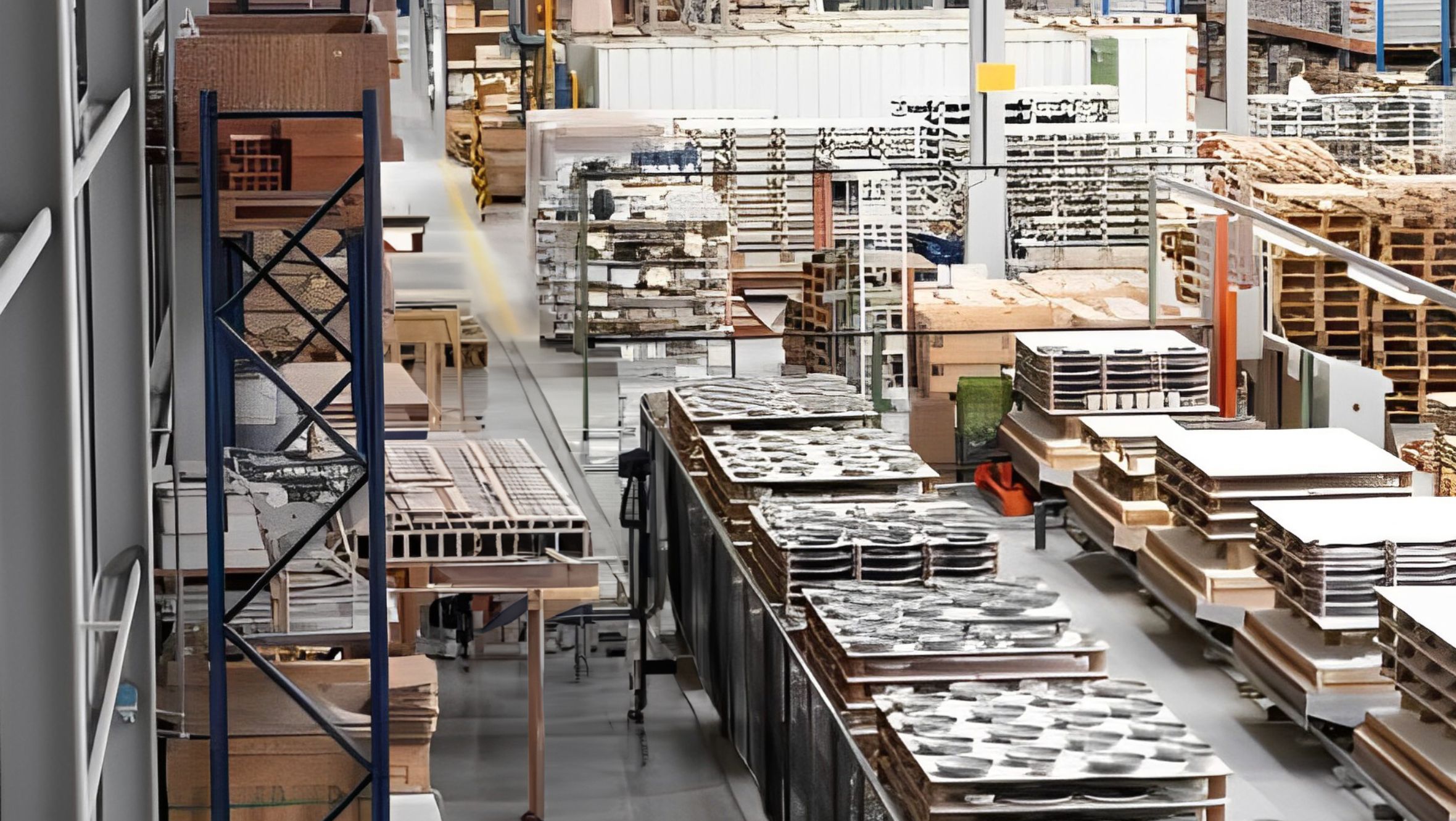